Hallo, Herr Tchigir, wir freuen uns sehr, dass Sie sich die Zeit genommen haben, mit uns über den Einsatz von Lean Management auf unserem Bauvorhaben Neustrelitzer Straße zu sprechen. Können Sie uns vorab noch einmal kurz erklären, was genau Lean Construction ist?
Lean Construction kommt von Lean Management und Lean Management kommt eigentlich aus der Lean Production und wird auch die „schlanke Produktion“ genannt. Das heißt ursprünglich ist das ein System von Toyota, entwickelt für die Automobilindustrie. Dann sind weitere Branchen, wie der Baubereich, sowie viele andere Wirtschaftszweige darauf angesprungen, haben gesehen, wie gut Lean Management funktioniert und die Grundprinzipien und Methoden für ihren Wirtschaftsbereich übernommen. Letztendlich ist das Ziel vom Lean Management die Steuerung und Organisation von Prozessen in einem Unternehmen und die Vermeidung von Verschwendung (von z. B. unnötigen Prozessen) sowie die kontinuierliche Verbesserung. Lean Construction, wie es u.a. im Baubereich heißt, wurde ursprünglich Ende der 90er Jahre in den USA entwickelt.
Was sind Ziele von Lean Management im Baubereich?
Ziele von Lean im Baubereich sind eine hohe Planungs- und Terminsicherheit zu haben, weil man ja die Prozesse alle von vorne bis hinten durchtaktet. Dadurch hat man eine hohe Transparenz, weil die Prozesse natürlich auch klar und verständlich für alle dargestellt werden. Man geht in eine detaillierte Prozessplanung und Arbeitsvorbereitung, was man unbedingt machen muss beim Lean und man muss relativ frühzeitig anfangen, sich damit zu beschäftigen. Vorteil dabei ist, man erkennt Planungsfehler und Ungereimtheiten vorzeitig und kann vielleicht noch gegensteuern. Durch diese Transparenz, die frühere Arbeitsvorbereitung und Prozessplanung hat man den Vorteil, dass Mängel und Kosten reduziert werden.
Welche Vorteile könnte der Einsatz von Lean Construction für ein mittelständisches Unternehmen, wie die BATEG es ist, noch mit sich bringen?
Letztlich gibt es da keine großen Unterschiede, das Bauvorhaben, was wir bauen, würde genauso ein Großkonzern bauen, die Vorteile sind für alle gleich: man hat einen geordneten Bauablauf und man hat Preis- und Terminsicherheit. Da ist es egal, ob ich nun einen Auftrag mit 100 Millionen Euro habe oder nur einen mit 10, 15 oder 20 Millionen. Oder ob ich 600 Wohnungen baue oder 105 Wohnungen, da ist nur das Volumen größer, aber Ablauf und Vorbereitung bleiben gleich und auch die Vorteile, die dadurch entstehen. Ich würde das gar nicht auf Mittelstand oder Großkonzern runterbrechen, sondern behaupten, dass Lean für jeden von Vorteil ist.
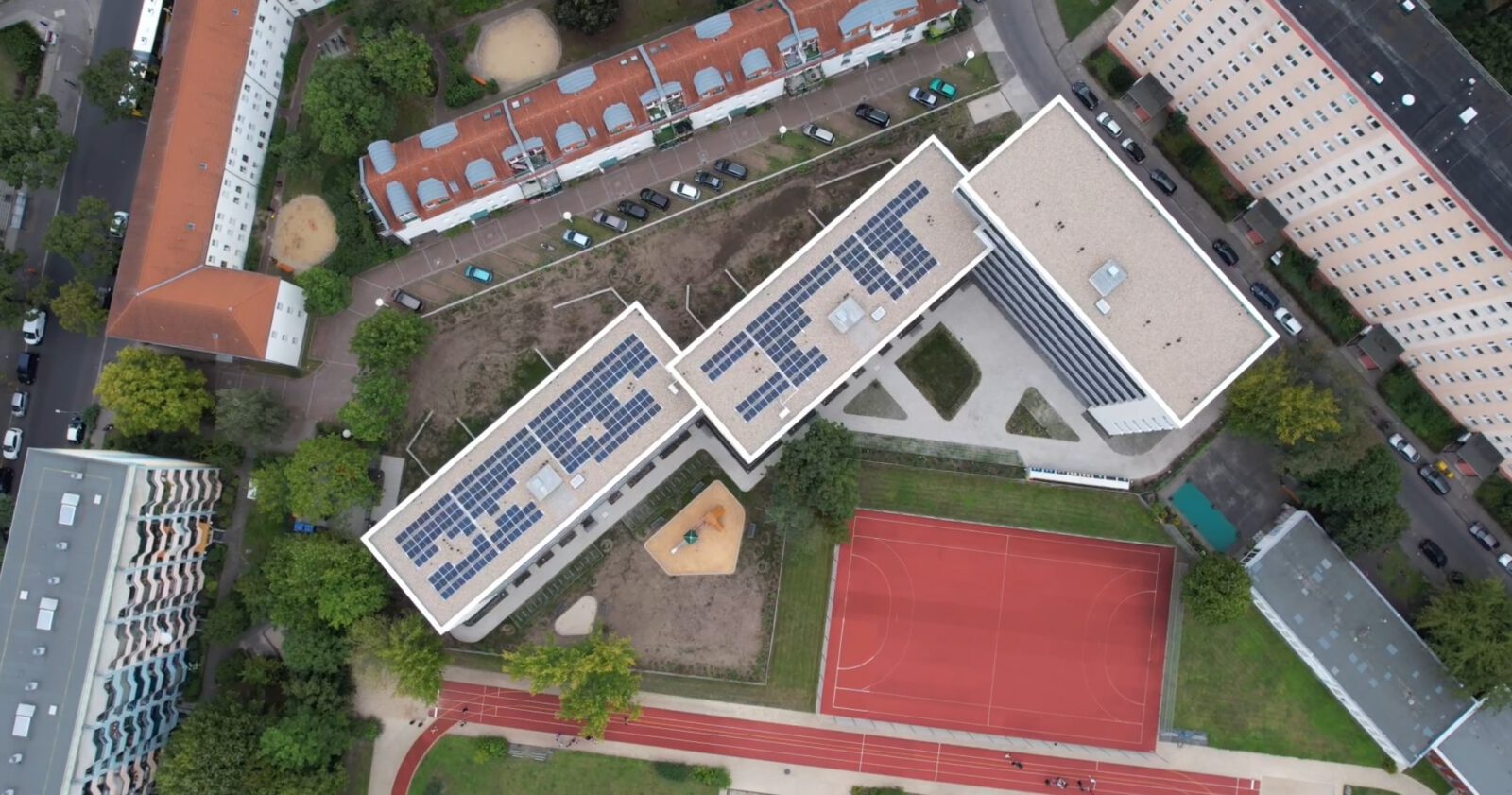
Was war eine besondere Herausforderung beim Einsatz von Lean Management auf unserer Baustelle in der Neustrelitzer Straße?
Die Herausforderung war – die gibt es aber überall – die Akzeptanz für etwas Neues zu schaffen. Die Akzeptanz hier bei BATEG war sehr gut. Unsere Geschäftsführung hatte das System schon einmal gehört und fand die Idee gut. Sie haben einem da einfach Vertrauen geschenkt und gesagt „ja, probiert es, wenn die Erfahrungen gut gewesen sind, wieso nicht“. Lean ist ja nichts anders als ein geordneter Bauablauf. Man baut nicht neu, sondern man strukturiert einfach den Terminplan anders.
Wie haben die Nachunternehmer den Einsatz von Lean Management wahrgenommen?
Wir hatten das Glück, dass mehr als die Hälfte der Nachunternehmer schon einmal mit Lean gearbeitet hatten. Die Hauptgewerke Heizung, Sanitär, Fliesenleger, Elektro und Trockenbau kannten Lean und hatten das alle als gut empfunden, somit waren sie dem gegenüber positiv eingestellt. Die Firmen, die noch nicht im Lean System gearbeitet haben, mussten entsprechend geschult und der Mehrwert aufgezeigt werden. Aber keiner war negativ eingestellt. Am Ende waren wirklich alle Nachunternehmer sehr zufrieden mit dem Ablauf und würden alle gerne noch einmal mit Lean arbeiten.
Sie sagten, der Einsatz von Lean braucht eine gewisse Vorbereitung, ist diese Vorbereitung sehr zeitaufwendig?
Ja, man muss sich frühzeitig damit auseinandersetzen und die Zeit dafür finden. Bei dem Projekt in der Neustrelitzer Straße hat das funktioniert, das wollte ich unbedingt mit Lean durchführen und habe mir die Zeit genommen. Am Ende erspart einem die intensive Vorarbeit viel Stress und Ärger.
Wieviel Zeit braucht man denn für die Ausarbeitung?
Man sollte mindestens ein halbes Jahr vor Beginn der Arbeiten mit der Vorbereitung beginnen. Wichtig ist es dabei die Nachunternehmer rechtzeitig mit in die Taktplanung einzubinden. So erhält man frühzeitig ein Feedback, wie realistisch die gesetzten Wochenziele sind.
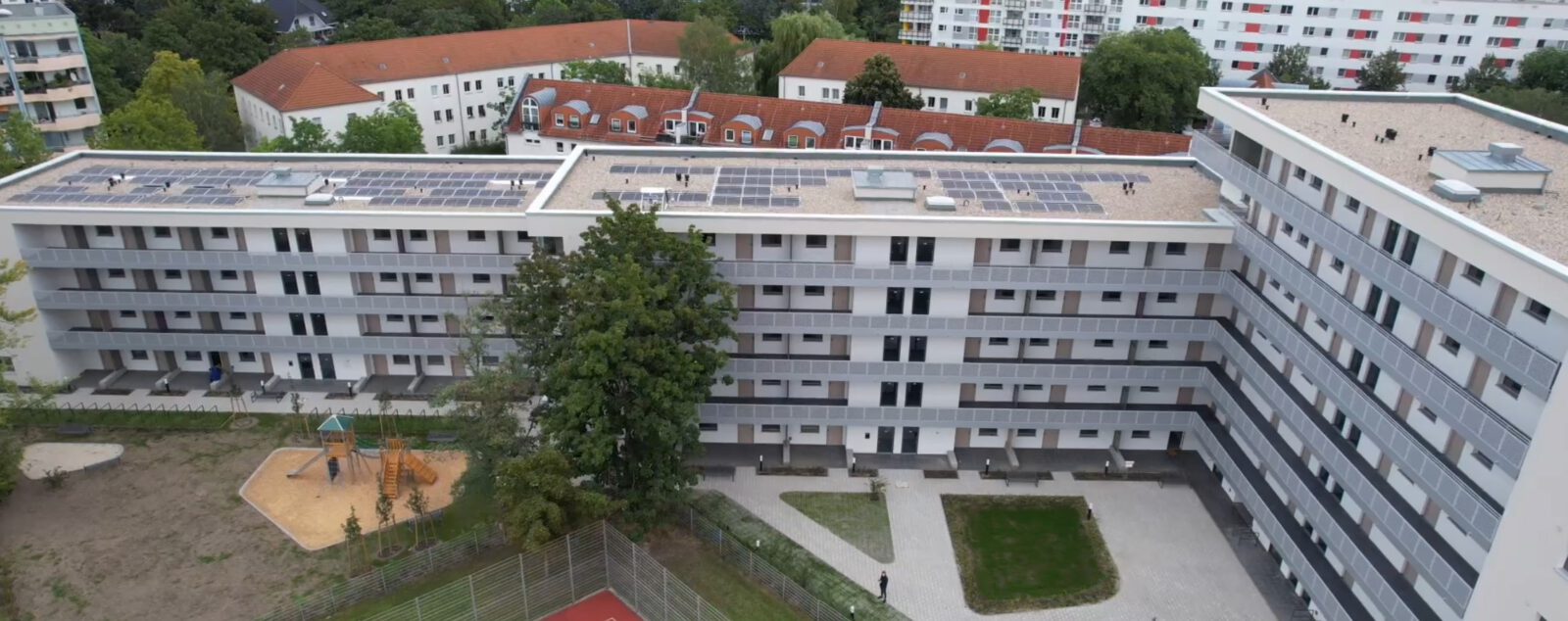
Das Potpourri an Lean Methoden ist riesig. Welche Methoden haben Sie auf der Baustelle in der Neustrelitzer Straße eingesetzt?
Eine Methode, die wir verwendet haben, ist z.B. die Just-in-Time-Produktion. Die Just-in-Time-Produktion zielt darauf ab, dass bei den einzelnen Produktionsschritten immer „die richtigen Teile am richtigen Ort, in der richtigen Menge, zum richtigen Zeitpunkt und in der richtigen Qualität“ vorhanden sind. In der Automobilindustrie wird vieles just-in-time angeliefert, um sich Lagermöglichkeiten einzusparen, sowie unnötige Transportwege zwischen Lager und Produktionsstätte zu vermeiden. So läuft Lean im Bauwesen auch ab, die Nachunternehmer kriegen ihre Materiallieferungen wochenweise, dass man nicht Unmengen an Material auf der Baustelle und es zum Tag der Ausführung am richtigen Einbauort parat hat. Oder das Entsorgungskonzept, das bei uns auf der Baustelle zum Einsatz kam. Die Zeit, die ein Handwerker braucht, um Materialreste einzusammeln und wegzufahren, ist alles Zeit, die er brauchen könnte, um produktiv zu sein. Das lagert man aus. Dazu hat man eine Firma, die die Bereiche reinigt und die Materialreste entsorgt. Dann gibt es das Fluss-Prinzip, das ist ein elementares Element von Lean Construction, dass man Takte, bzw. sogenannte Gewerkezüge bildet. Man versucht das Prinzip einer Fertigungsstraße aus dem Automobilbau auf die Baustelle zu übertragen. Durch Kopplung und Ausrichtung der Prozesse laufen die Gewerke in einer festen Reihenfolge durch das Gebäude bzw. durch die festgelegten Taktbereiche, ohne dass sich dabei Fehl- und Wartezeiten ergeben. Durch das Fluss-Prinzip entsteht also ein „fließender“ Bauablauf in Form eines Zuges, der sich durch das Gebäude bewegt. Mittels Takt-Prinzip wird eine gleichmäßige Geschwindigkeit aller Gewerke garantiert. Realisiert wird dies durch Abstimmung und die Harmonisierung der Gewerkekapazitäten. Üblicherweise wird bei Lean Construction-Bauvorhaben eine Taktzeit von fünf Arbeitstagen gewählt, d.h. innerhalb dieser Zeit muss ein Teil- bzw. Taktbereich fertig gestellt werden.
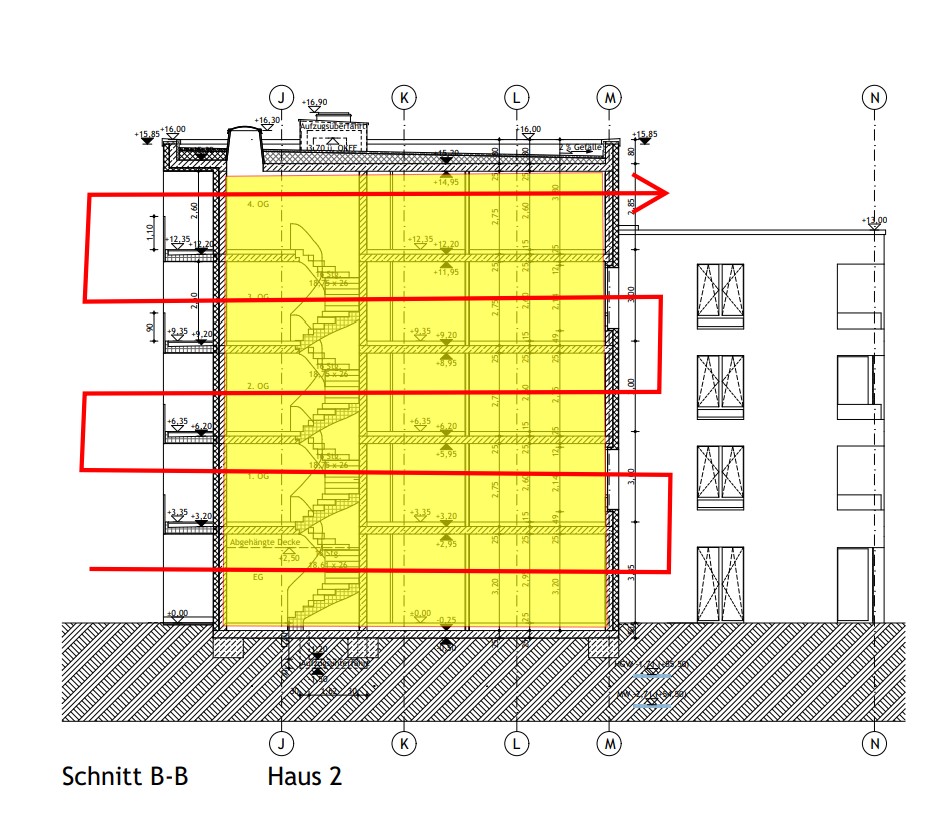
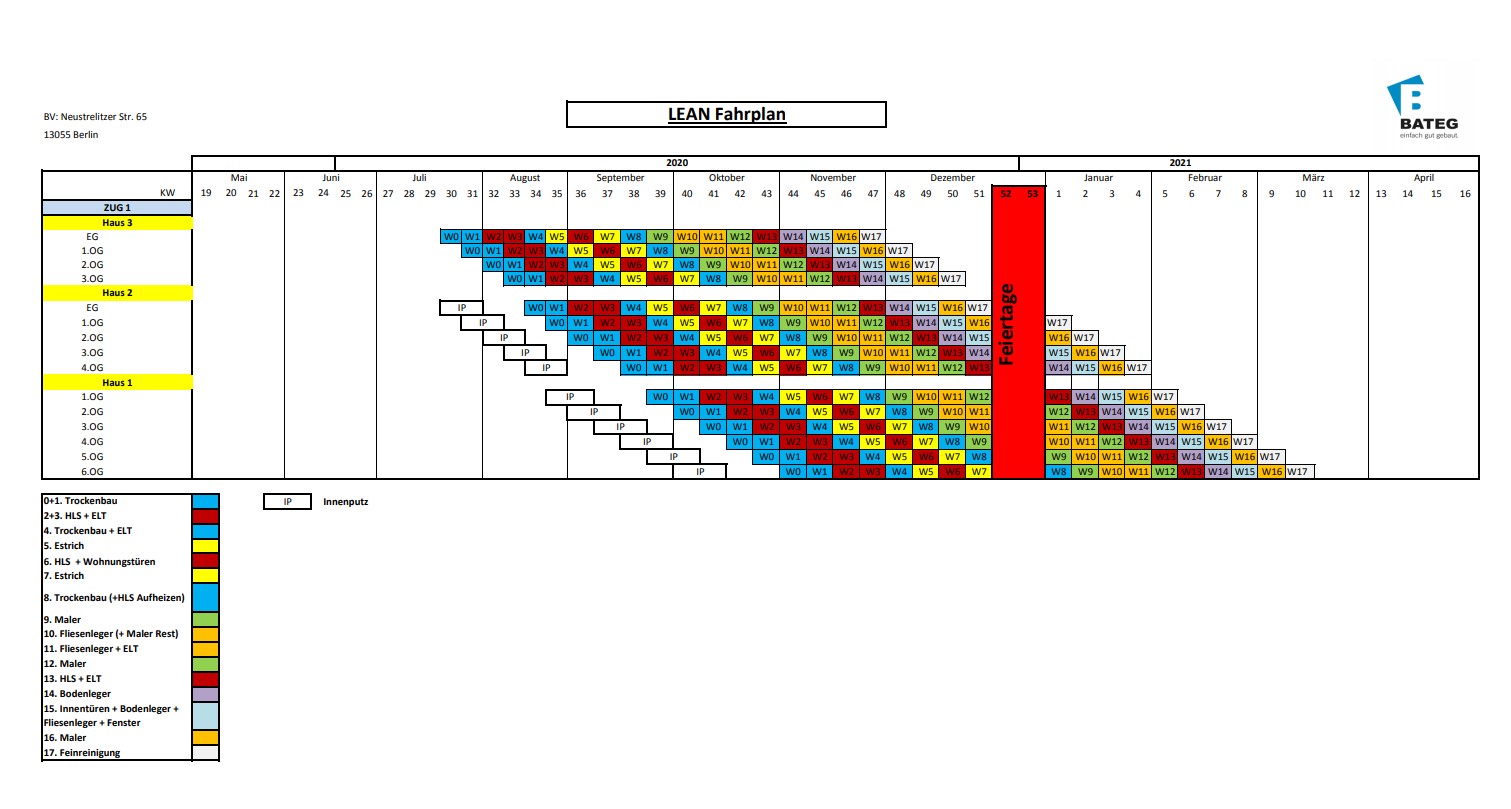
Lean Meetings sind ebenfalls fester Bestandteil der Methode, was unterscheidet sie von anderen Besprechungen und in welchen Intervallen fanden sie statt?
Normalerweise ist das so, man hat einmal die Woche ein Baubesprechung, die geht zwei Stunden und jeden Nachunternehmer betrifft das Thema aber nur 10 Minuten und danach sitzt man die Zeit ab. Hier haben wir es so gemacht, dass man die Besprechungen auf maximal 15 Minuten reduziert hat, um auch nur die wichtigsten Themen zu besprechen, sowie den Status der Fertigstellung der Taktbereiche abzufragen. Die Meetings fanden meistens auch nicht im Besprechungsraum statt, sondern draußen auf der Baustelle. Wir haben eine große Tafel gehabt, wo der Lean-Fahrplan abgebildet war und wir hatten die Taktplanung, einen Übersichtsplan des Bauvorhabens, angebracht. Durch die offene Kommunikation konnten Probleme angesprochen und in den meisten Fällen schnell gelöst werden. Am Anfang haben wir uns täglich getroffen, das ist dann mit der Zeit auf drei Mal pro Woche runtergegangen, zum Ende hat man sich einmal pro Woche gemeinsam abgestimmt.
Der Lean Ansatz sieht eine engmaschige Überprüfung, aller auf der Baustelle stattfindenden Prozesse, vor. Das klingt für Außenstehende nach Mehrarbeit. Stimmt das?
Ich würde sagen, am Anfang ist es mehr Arbeit, zum Ende hin wird es weniger, weil der Wiederholungseffekt eintritt und die Nachunternehmer genau wissen, worauf sie achten müssen. Wenn Fehler entstehen, dann entstehen sie am Anfang, beim ersten Mal der Ausführung. Danach sollte eigentlich alles klar sein, es gibt dann höchstens Mängel, wenn unsauber gearbeitet oder etwas falsch gebaut wird. Was aber auch weniger ist, weil durch die sich ständig wiederholenden Prozesse, das Risiko für Mängel minimiert wird. Man muss dann vor allem kontrollieren, dass der zeitliche Rahmen eingehalten wird und ggf. Maßnahmen ergreifen.
Sie sagten, in Konzernen wird im Lean Management schon eine Software eingesetzt, wäre es denkbar, Lean bei BATEG auch softwaregestützt einzusetzen?
Es gibt die Idee, es gibt ja auch verschiedene Anbieter, die sowas schon anbieten, es macht glaube ich aber erst Sinn, wenn schon mehrere Baustellen mit Lean arbeiten. Im jetzigen Rahmen geht es vorerst so. Wir müssen das Lean Construction zunächst bei BATEG etablieren. Dann ist der Einsatz von bestimmten Softwarelösungen sicherlich sinnvoll.
Wenn Sie Ihre Erfahrungen mit dem Einsatz der Lean Methode auf der Baustelle in der Neustrelitzer Straße resümieren, könnten Sie sich vorstellen, Lean auch für künftige Projekte bei uns einzusetzen?
Definitiv, aber es kommt immer auf das Projekt an, es muss einen hohen Wiederholungsgrad in dem Bauvorhaben geben, dann kann man es anwenden. Lean Construction lebt davon, dass es einen Wiederholungseffekt gibt, dass ein Automatismus reinkommt, dass die Leute das wie im Schlaf anwenden. So wie in der Automobilindustrie ein Fließband läuft, wo der eine Mitarbeiter immer nur die Tür anschrauben muss, und dann läuft das Auto weiter und der nächste baut den Sitz ein. So ungefähr kann man sich Lean auch auf der Baustelle vorstellen, dass die Gewerke von einer Etage in die nächste gehen und immer das gleiche machen. Das funktioniert im Wohnungsbau sehr gut, im Mietwohnungsbau vor allem, bei Hotels, Bürogebäuden oder in Altenheimen könnte ich mir das auch vorstellen.
Wäre es denkbar auch andere Mitarbeiter in Lean zu schulen?
Für jeden Mitarbeiter wäre das von Vorteil, es muss natürlich die Bereitschaft da sein. Gleichzeitig muss es jemanden geben, der diese Schulungen durchführt und die Mitarbeiter berät. Eine reine Schulung wird nicht viel bringen. Man muss jemanden haben, der sich damit beschäftigt, der das schult und der auch bereit ist, Projekte mit anzuschieben. Man muss Lean leben, eine wirklich gute Vorbereitung treffen. In der Ausführungsphase da hinterher sein, dass die abgestimmten Taktzeiten eingehalten werden, alle Arbeiten abgeschlossen sind und das den Firmen auch verständlich machen. Das war am Anfang manchmal etwas schwierig, aber die Firmen merken schnell den Vorteil, wenn sie in einen neuen Taktbereich kommen und sehen, da ist keiner, da ist alles sauber. Dann versuchen sie ihre Leistung auch zu schaffen. Am Ende waren alle im Plan und auch sehr zufrieden, es wird wahrscheinlich nicht das letzte Projekt sein, das wir mit Lean machen werden.
Herr Tchigir, wir danken Ihnen für dieses Gespräch.